
An Overview of Polypropylene Thermoforming Process

Polypropylene was first polymerized in 1951. Since then it has become one of the most commercially used thermoplastic polymers. Today thermoforming polypropylene has become a great option for manufactures. The main reason is its versatility and low cost.
In this article you will gain insight into the manufacturing process of propylene, the complete polypropylene thermoforming guide. You will explore the process challenges that will face you. Finally you will learn how to connect with the right polypropylene suppliers.
1. What is Polypropylene, what is used for?
Polypropylene (PP) is a crystalline thermoplastic that manufacturers use widely in everyday products and applications such as household products, packaging trays, medical devices. The PP is used widely in commercial production, as it has special qualifications, such as chemical resistance, flexibility, low electrical conductivity, safety to use on food, low water absorption, and the important one that is PP keeps products’ costs low.
Propylene is used for products for large sectors such as machinery and textiles and even fibers. The pp material will see growing demand globally as the PP resins are replacing metal material in the automotive and the medical sector.
2. What is polypropylene made from?
Plastics are generally derived from natural materials such as crude oil, cellulose, coal, natural gas, and salt. It is produced through two main processes polymerisation and polycondensation.
The polypropylene resin is built by up polymerization of propylene and is considered one of the most important polyolefin family resins. Propylene itself is obtained by the thermal cracking of propane, butane, ethane, and the naphtha fraction of petroleum.
3. Polypropylene thermoforming process
Thermoforming is a process that involves some steps:
- Heating the plastic sheet to be soft or malleable depending on the specific temperature range.
- Stretching the Plastic sheet against a cool single-sided mold.
- Cool the sheet to the point that we can retain the shape of the mold.
So, PP thermoforming process is a group of sheet-forming processes to reach the best shape for the final plastic products.
4. How do you thermoform polypropylene?
To thermoform propylene, you can use a vacuum forming process, this vacuum is formed between the thermoplastic sheet and the mould cavity.
- First, the thermoplastic sheet is clamped.
- Second, the sheet is heated to a softening temperature, (165-140 °) is the suitable temperature range to thermoform propylene.
- Third, the sheet of propylene is clamped in the frame.
- Fourth, the vacuum is turned on and pumps out all the air, here the shape of mould can be seen clearly.
- Finally, the plastic cooled, then the vacuum pumps switched off, and the excess plastic shape remains.
5. What are the methods of forming?
Vacuum forming is not the only method to form plastic raw material, such as propylene. The vacuum is the simplest one but also there are two other types of forming:
Twin Forming: in twin forming, there is no room for experiment or errors, as the plastic requires more care and precision, it is about heating two plastic sheets at the same time, fitting them, and finally fusing them, and there are pressed points the plastic must be matched with, if any error happened, it will affect the product integrity, cause the twin sheet must be ideal and double-wall, to form final products such as fuel tanks, and air ducts.
Pressure Forming: this type of forming allows the manufacturers to achieve higher levels of sharp edges than vacuum forming, the process begins after the polypropylene is fitted around the tool, then they blasted the plastic at high temperature with air and pushed against the tool to create the final shape design, it is used for manufacturing medical equipment such as medical laser assemblies, and x-ray scanners.
6. How to determine the right polypropylene thermoforming temperature?
The thermoforming temperature depends on the type of the material and when it comes to propylene the perfect temperature for PP thermoforming is from 165 ˚ to 180 ˚C. But we have to say that the ideal temperature depends on the plastic sheet thickness, the type of mold, and the machines.
7. What are PP Processing challenges?
PP has such great properties, as fatigue resistance, heat resistance, chemical resistance, translucency, and toughness, but there are challenges you will face while using PP material, such as:
Low-melt strength: It causes sagging and sheet thinning during thermoforming.
Narrow temperature range: PP requires careful monitoring for successful thermoforming.
Long time for crystallization: PP to fully crystalize takes a long time which can affect the production cycle.
Unevenly shrinkage: that problem can cause warpage on the final part.
But you can solve these problems by increasing the crystallinity level, and small spherulites presence.
8. How to connect with quality polypropylene suppliers?
"Gap Polymers" suggests 5 tips for your sourcing strategy to help you identify the best PP granules suppliers:
1- Certification
There are a lot of certifications you can rely on while choosing the best suppliers such as:
AEO: The AEO certificate is one of the most important certificates that based on the customs business partnership. It introduced by the World Customer Organization (WCO).
ISO: This certification includes the manufacturing process, management system, service, or documentation. It certifies that the supplier has all the requirements for quality insurance and standardization.
2- Customer Service
Choosing the best supplier does not only depends on purchasing but also continues to customer service. After purchasing you may need technical support to ask about process optimization, material selection, and components designs.
3- Align shipping locations to your needs
Shipping is a big matter, so you must choose the best shipping method for you and your clients. You must choose the shipping service that can be tracked right to your destination.
4- One Stop Shop
You must choose the supplier that can offer multiple plastic products and multiple services such as technical support. The one stop shop strategy will support you with efficiency and convenience.
5- Flexible Payment
It allows you to purchase plastic products and pay for them over time according to your needs. You’ll need to decide which payment method you will choose between cash, checks, debit cards, etc.
Subscribe to get access to all the new articles, blog posts, industry updates and trends, and more.
Suggested Blogs

Exclusive vs. Non-exclusive Distributor
GAP Polymers Team
Have you ever wanted to know the difference between the exclusive and the non-exclusive polymer distributers, GAP polymers will help you to know the main differences between them.

Weekly Plastic News & Resins Pricing
GAP Polymers Team
A weekly coverage of all you need to know about the international plastic industry including resin pricing, trends, market insights, and more.
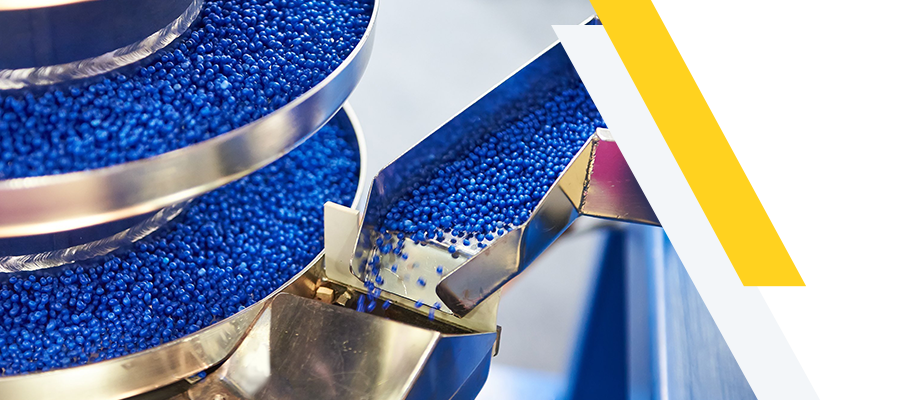
A Deeper Look Into Plastic Manufacturing Industry
GAP Polymers Team
Keep up with the rapid changes of the plastic manufacturing industry and dive deep into what shapes the polymer industry and how to choose the best raw material supplier for your business.
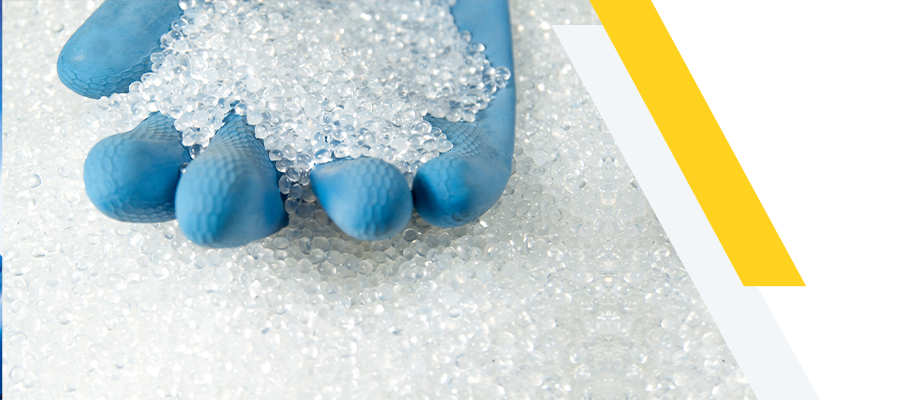
Polymer Industry Updates: What's coming up in 2023?
GAP Polymers Team
2023 is a critical year in the polymer industry at all levels. Global polymers market size is expected to grow finally after the economic recovery from the pandemic.
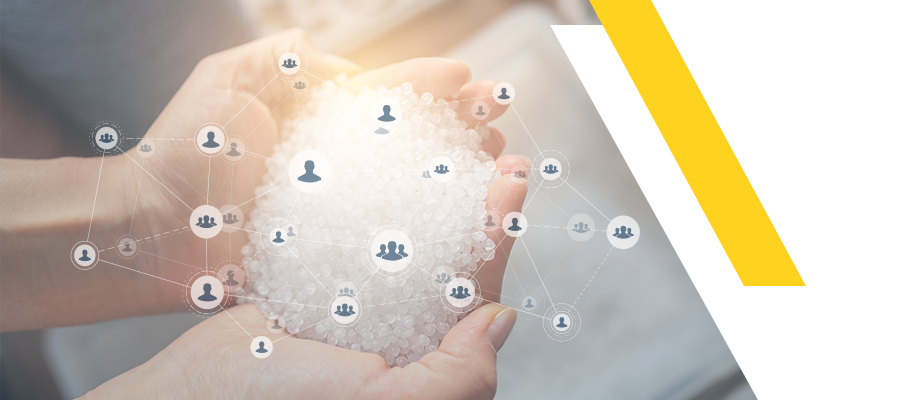
Top Plastic Raw Material Suppliers
GAP Polymers Team
The polymer industry is facing continues challenges and choosing the best supplier is getting harder. Look no further and explore the full list of the top plastic raw material suppliers.
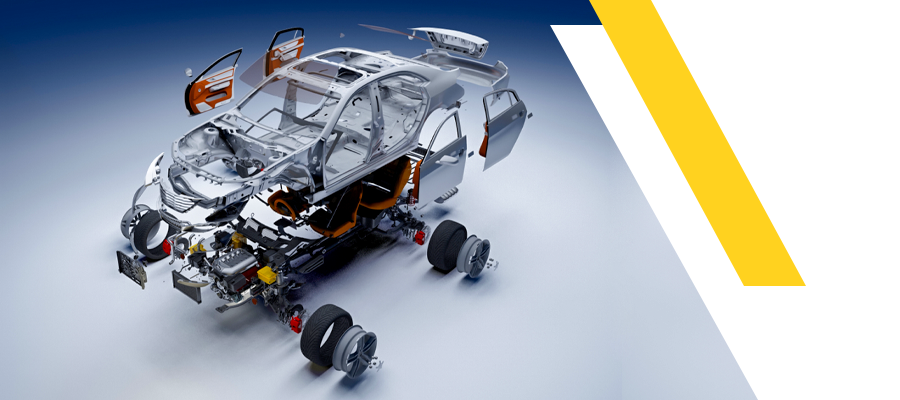
5 Polymers Used in the Automotive Industry
GAP Polymers Team
Plastics industry has changed the method of manufacturing cars. Now you can explore which material are used in automobiles and how automotive plastics affects demand in the polymer industry.