
HDPE Resins: A Multi-Purpose Thermoplastic

High-Density Polyethylene is a thermoplastic polymer known as the HDPE plastic or plastic number "2". As its density ranges from 930 to 970 km/m3, it is known for its high strength-to-density ratio.
This plastic material made from thermoplastic polyethylene requires 1.75 kilograms of petroleum to provide the raw materials for one kilogram of HDPE. High-Density Polyethylene (HDPE) is usually recycled and widely used in many plastic applications. In 2007, its traded quantity in the world reached 30 million tons.
The global resin market for high-density polyethylene (HDPE) reached a value of about USD 70.7 billion in 2021. The market is further expected to grow at a CAGR of 4% in the forecast period of 2021-2026 to reach a value of approximately USD 89.5 billion by 2026.
To get the overview about HDPE Resins properties and uses, we will cover the following points and questions:
-
How is HDPE Resins made?
-
Why is HDPE important?
-
How to color HDPE?
-
How to mold HDPE plastic?
-
Is HDPE plastic safe / food contact plastic?
-
How is HDPE plastic recycled?
-
What are HDPE Injection molding applications?
-
Summary about HDPE Resins
1- How is HDPE Resins made?
While plastic manufacturing process include plastic injection and blow molding to produce high-quality plastic components. HDPE manufacturing process focuses on “Cracking” when HDPE is exposed to intense heat under controlled conditions, the cracking process helps create ethylene gas molecules that form polymers.
Then the polyethylene is put through a series of molds to form into granules, here you can identify the HDPE in its final appearance.
To be more specific, the manufacturing process includes 5 phases, polymerization with the comonomer and hydrogen, drying when the wet powders are transferred to powder drier, Extrusion when the material is melted and pelletized in the extruder, then they are transferred to the storage silo, and finally the packaging when the material is cooled by air and stored.
2- Why is HDPE important?
HDPE raw material is important because of its advantages:
- Sustainability
HDPE is sustainable because of many reasons. It is made from recycled materials. It is 100% recyclable. It is lightweight.
- Resistance
HDPE is resistant to gentle oxidants, strong acids, and reducing agents. It has more chemical resistance than LDPE (Low Density Polyethylene). It has high resistance to environmental impacts such as insects and moisture.
- Flexibility
HDPE plastic is very flexible, so manufacturers can shape it to make a lot of applications. Manufacturing HDPE does not need special tools.
- Food safety
HDPE does not have Bisphenol A (BPA), which makes it perfect for food packaging and producing food containers.
3- How to color HDPE?
Colored HDPE has the same properties as HDPE normal sheeting. Natural HDPE has semi-translucent color. You can color HDPE plastic by fusing different colored sheets together. Colored HDPE is very suitable for outdoor applications, as the color will not delaminate, warp, or crack.
HDPE can be colored by the pigmentation process when color goes through the entire sheet.
The surface coating is not the best way to pigment HDPE, as the color could flake off or scratch.
4- How to mold HDPE plastic?
HDPE is a soft polymer. It loses its rigidity and begins to melt at 125°C.
Injection molding is the best way to produce HDPE as it costs low, and can create different project specifications, and quicker than all other molding processes, and produces a higher volume of products.
Here are the steps to mold HDPE:
- Reaching the ideal temperature in the injection molding machine, to transfer it to types into the cavities.
- Cool the shape of the mold and eject the parts that are fully set.
- Resetting the mold to make other parts and repeating the process.
5- Is HDPE plastic safe / food contact plastic?
When it comes to food safety, HDPE is divided into 2 types:
- Virgin HDPE: The virgin HDPE is safe plastic for food contact, so it is suitable for making food containers. it does not absorb moisture.
- Recycled HDPE: The recycled type is reviewed by the food and drugs administration case by case basis.
HDPE, which is also known as plastic number 2, is safe for use with food, especially in long-term food storage.
6- How is HDPE plastic recycled?
HDPE recycling can be done in several phases:
- HDPE is separated by grade according to its durability and thickness and other variables.
- Cleaning HDPE to remove wrecks to be available for processing.
- HDPE is ready now to enter the granulation process by melting larger pieces of the plastic into granules or shredding them down
- Reshaping the granules to create various products.
According to plastic experts, the recycling rate of HDPE natural bottles was 29.3% in 2018, 12% of all HDPE plastics are recycled and 28% of milk jugs are recycled.
7- What are HDPE Injection molding applications?
HDPE has ideal properties that can make it perfect for daily use applications such as:
- Toys
- Plastic bottles
- Food storage containers
- Plastic chairs and bottles
- Plastic milk jugs
- HDPE is also used in other products such as:
- Plastic pipes
- Hard hats
- Recycling Bins
- Grocery Bags
8- Summary about HDPE
Physical Properties of High-Density Polyethylene Resin
Property |
Metric units |
Melt Temperature |
130°C |
Tensile Strength |
20 MPa |
Flexural Strength |
21 MPa |
Shrink Rate |
1.7-2.9% |
Specific Gravity |
0.95 |
Recycling ID |
2 HDPE |
Click Here to get your quote for HDPE resins supplying today! |
Suggested Blogs

LDPE: Best Solution for Shrink Film and Packaging
GAP Polymers Team
LDPE material is one of the more economic types of polymers known for its flexibility, moisture, and chemical resistance. It is commonly used for shrinking film and packaging applications.
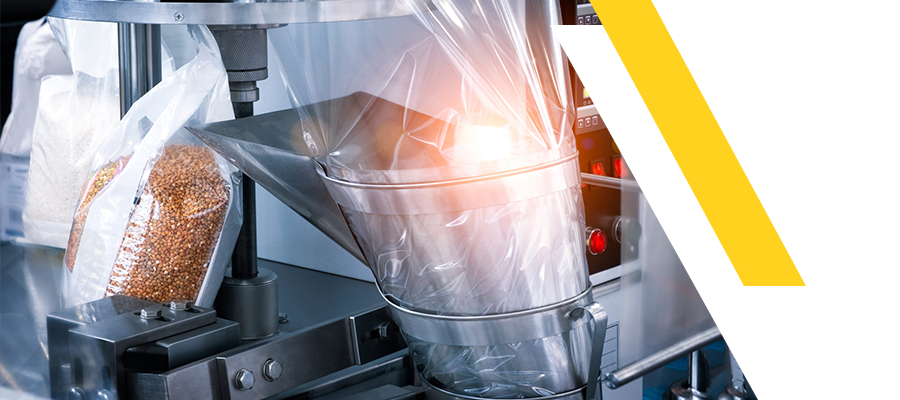
Polyethylene Plastic: HDPE vs LDPE vs LLDPE
GAP Polymers Team
Polyethylene is the one of the most common used plastics. Find an in-depth examination for the three classification of PE to choose the right material for your packaging application.